A lot of people don’t realize that stainless steel is one of the most used materials across a wide range of industries, mostly because it’s incredibly tough and durable, as well as resistant to corrosion. Additionally, when compared to other materials and metals, when exposed to extreme environments, stainless steel won’t break or fail.
Whether you’re a student that needs to learn more about the casting process of stainless steel or if you simply want to understand it better for your own projects, our 2024 guide from below can help! Before we take a look at the top six tips that can help you understand the overall process of casting this durable material, let’s first look at what it is:
One of The Toughest Material Out There: Explained
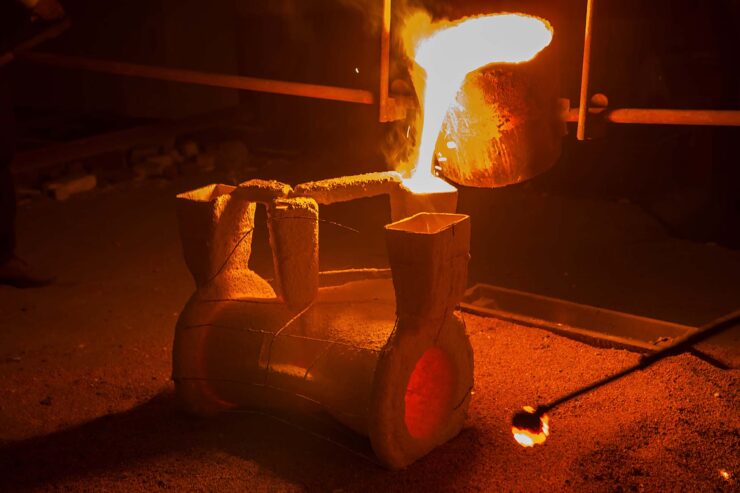
To put it as simply as possible, stainless steel is essentially a mixture of carbon and iron – just like many other metals and alloys out there. But, the one thing that makes it different is that it’s also combined with chromium. This particular material is added to the mixture to ensure that the metal is more resistant to oxidation, thus, manufacturers ensure that there is at least 10 percent of chromium in the mixture.
According to a stainless steel casting company called DawangCasting, Chromium is responsible for creating the so-called “passivation” layer that has regenerative properties if the surface gets scratched or damaged. There are two processes that can be used for creating stainless steel, wrought and cast. Casting the material is most commonly used and it’s easier for producing complex designs and shapes. Here are our eight tips that can help you understand this somewhat difficult process:
1. Molds Have to Be Prepared
As you might have guessed from the name, casting will require liquid metal to be poured into a container, and because of this, the first stage of the entire process is creating and preparing the molds. Of course, they’re designed and manufactured in the shape of the items that have to be made and when it comes to creating complex shapes, the molds cannot be made from one piece, instead, they most commonly come in pairs. Once they’re assembled, the cavity within the mold will have the shape of the item being made.
There is a wide range of materials that they can be manufactured from, however, industrial wax is used more often than materials such as plastics, due to the fact that they’re simple to melt and reuse, thus, making the whole process less expensive. Once they’re manufactured, they go through inspection so that the company manufacturing the item can ensure that there are no mistakes and flaws in the design.
2. Next Comes Sand Shelling
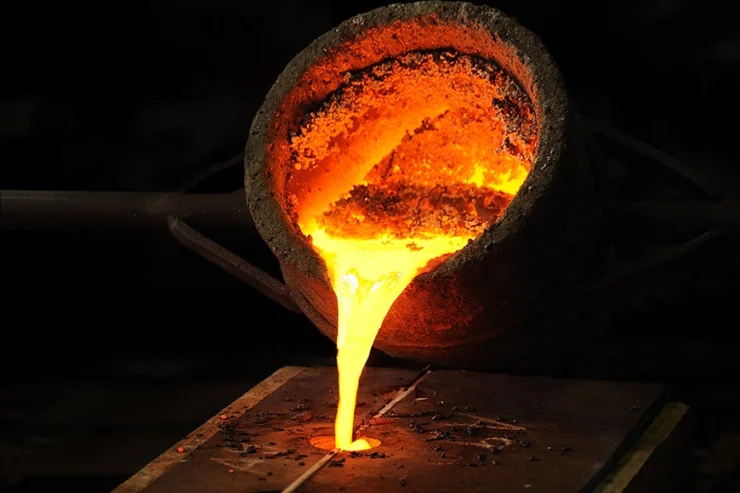
When the mold is completed, the wax is melted, and later on, you’ll be left with a sand shell, which is essentially the mold where you’ll pour the liquid metal. Once it’s coated, it’ll be prepared for baking. Industrial wax can be melted at approximately 150ºC, and once it does, you’ll be left with a hollow sand shell. The shell is then processed and baked once more but at a higher temperature, thus, in the end, it’ll be durable and tough enough so that you can pour the liquid metal into it.
3. Pouring Needs to Be Done While The Shell is Hot
While the aforementioned shell is still hot from being processed, it’s transported to the area where the metal will be poured. It’s crucial that it’s hot, mostly because it’ll guarantee that the steel enters all areas of the cavity. You must know, physical items expand and shrink under cold and hot temperatures, thus, contracting of the shell must be avoided during the stages of cooling. Also, the process does look like nothing can hinder it, however, there is no room for errors since the whole process will fail otherwise.
4. The Mold is Manually Broken
When the metal is cooled and solid, the shell must be broken. In most cases, it’s done manually with a hammer or other similar tools. Once you break the shell, you’ll be left with the stainless steel cast which needs to be separated into several components. Keep in mind that all of the parts have to be polished and once this process is completed, they’ll be sent to the inspection area for locating any possible flaws in the design.
5. Inspecting The Finished Item
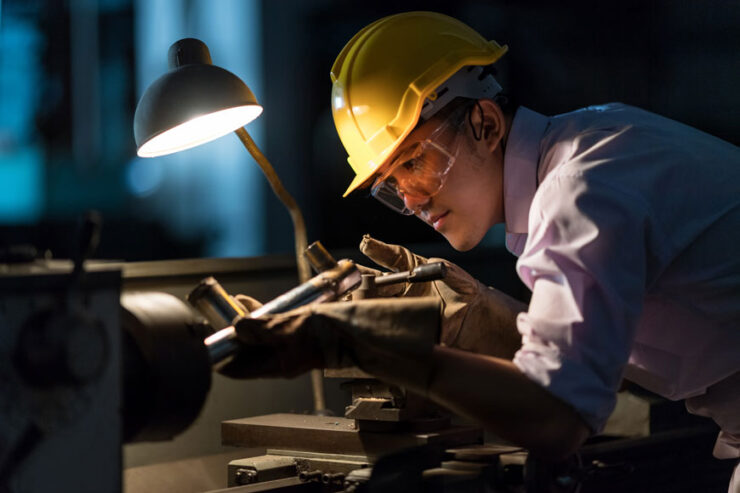
If the cast was properly separated, the components are then tested and inspected for any flaws, which can include things such as air holes or sand. Some defects, especially the smaller ones can be fixed by welding the metal, however, if there is a larger flaw in the design, the components are usually cleaned and then melted again. This ensures that the company casting the item saves money instead of using new steel for the process.
6. You Must Use Safety Gear
Before we conclude this 2024 guide, it’s crucial that we mention another important tip. If you’re planning on casting stainless steel on your own, you should, under no circumstances, do it without protective gear. After all, you’ll be exposed to extreme temperatures, and without wearing proper safety and protective gear, you could end up getting seriously injured, thus, before even attempting to cast something, you should purchase the items you need.
You’ll want to wear gloves and boots resistant to heat in case there are sparks or bursts of flame while melting and/or pouring the material. Additionally, you should purchase an apron that is thicker and resistant to heat, and by wearing it, you’ll keep your upper body protected while working on your project. Protective glasses are also a must, especially since if you don’t wear them, you could end up seriously injuring your eyes.
Conclusion
The whole process of casting stainless steel can be daunting and complex, especially if you have never done it before. However, with the right tips in mind, it’ll be easier for you to understand how it’s done, thus, no matter why you wanted to learn more about it, our tips from above can help.
By now, you most likely understand the whole process better, and if so, you shouldn’t lose any more of your time reading guides similar to this one. Instead, you might want to go through our article one more time, and don’t forget to watch some videos to see what it looks like!